Published: 10 July 2025
As mining operations evaluate the shift to autonomous technologies, the focus often lands on future-forward benefits: increased productivity, improved safety, and optimized efficiency. But in the drive toward autonomous mining, many overlook a powerful value lever that already exists on-site—the mixed fleet already operating on-site.
In today’s capital-intensive mining environment, the ability to retain and retrofit existing haul trucks—regardless of OEM—isn’t just convenient. It’s a strategic, cost-efficient path to open autonomy.
Unlocking Value from Your Existing Fleet
Across the globe, most large-scale mining operations run mixed fleets assembled over decades. One site might operate Caterpillar 793s, Komatsu 930Es, and Liebherr T 282s—each selected to align with site conditions, procurement cycles, or strategic partnerships.
Every one of these haul trucks represents a multimillion-dollar investment with a service life of 15–20 years. With an average fleet age of 8 years, many mines hold hundreds of millions in unrealized value.
Yet, closed autonomy ecosystems often demand a standardized fleet—forcing premature write off functional assets.
The Real Cost of Fleet Standardization
Let’s consider a common scenario:
A fleet of 40 haul trucks, each with a remaining book value of $2 million, equals $80 million in assets. To transition to a single-vendor autonomous fleet, a mine may face three costly decisions:
- Immediate replacement – Write off $80M and spend up to $200M on a standardized fleet
- Gradual Transition – Run dual systems for years, limiting efficiency gains
- Delayed autonomy – Wait for natural fleet turnover, risking competitive lag
Open autonomy eliminates these roadblocks by enabling autonomous retrofits across brands—preserving capital, accelerating ROI, and reducing transition friction.
Market Dynamics and Negotiating Power
Mixed fleet retention also sustains an often-overlooked strategic asset: negotiating power.
Standardizing on a single autonomy provider narrows vendor options and weakens price leverage. In contrast, open autonomy keeps the competitive field open—allowing mines to source equipment, parts, and services from the most suitable vendors at every procurement stage.
This flexibility is especially valuable during expansions or market shifts, where OEM availability, pricing, and technology leadership can vary. Closed-stack autonomy can limit choices; open systems keep doors open.
The Operational Continuity Factor
The benefits of mixed fleet retention go beyond dollars and cents. It preserves:
- Technical training
- Spare parts inventory
- OEM-specific maintenance procedures
- Deep institutional knowledge and site expertise
Closed systems often require abandoning this intellectual capital. Open autonomy builds on what’s already working—turning diversity into operational resilience.
The Integration Challenge
Adapting different OEM vehicles for autonomous operation isn’t without complexity. Each brand uses unique drive-by-wire protocols, sensor configurations, and safety systems.
The management overhead can be significant. Instead of training operators on one autonomous system, mines must maintain expertise across multiple platforms. Troubleshooting becomes more complex when issues could stem from OEM-specific implementations or integration layers. System updates must be carefully orchestrated to maintain compatibility across the mixed fleet.
While this complexity is real, it's not insurmountable—nor unprecedented. Recent progress, including the publication of ISO 23725:2024, provides a framework for enabling safe, coordinated behaviour between autonomous mobile equipment from different manufacturers. As standards like this gain traction, the barriers to integration are lowering, making cross-OEM autonomy a more attainable and less risky endeavour for forward-looking operations.
The True Cost of Open Integration
Industry estimates suggest that multi-vendor integration adds 15–25% to upfront implementation costs compared to single-stack autonomy. But when measured against asset preservation, the math is compelling:
- Integration cost: +$20 million
- Fleet value preserved: $80 million
- Net benefit: A compelling win
Of course, these figures are directional and should be evaluated within each operation’s specific context. Risk-adjusted modelling, including downtime scenarios and support contingencies, is essential. However, even under conservative assumptions, the capital preservation enabled by open autonomy often outweighs the integration premium—especially when paired with phased deployment strategies that mitigate risk.
Moreover, these integration costs are typically one-time investments. Once interoperability is in place, the ongoing complexity becomes part of standard operations—managed like any other system in a modern mine.
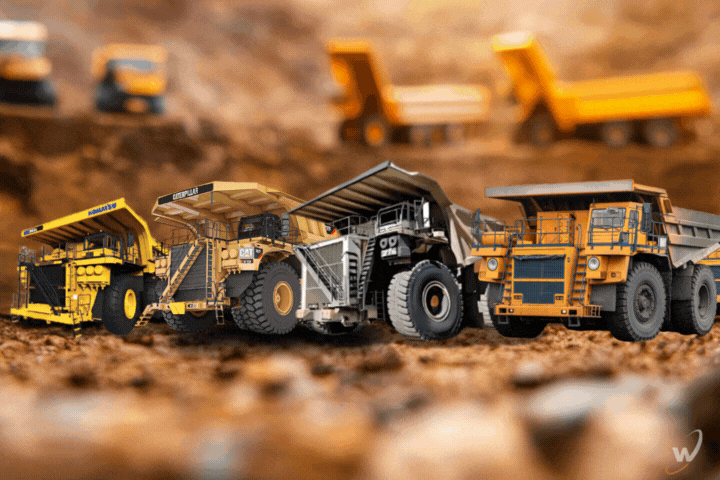
Is Mixed Fleet Retention a Temporary Fix?
Critics might argue that mixed fleet retention is merely a transitional benefit—important for the near term but diminishing in value as mines eventually standardize their fleets through natural replacement cycles. In such instances, open autonomy facilitates this transition on the mine's terms, allowing for a gradual, economically rational evolution, preserving flexibility rather than an overhaul. Nevertheless, the mining industry's history suggests that fleet diversity is not a temporary condition but a persistent operational strategy.
Even as autonomy gains traction, mixed fleet management will remain and for good reasons—driven by site-specific constraints and needs, procurement timing, geographic factors, service availability and the need for operational agility in volatile markets. Open autonomy doesn’t prevent standardization; it simply doesn’t require it.
That said, we must acknowledge that some operations might genuinely benefit from standardization. A new mine starting with a clean sheet might find the simplified operations of a single-vendor autonomous solution appealing. Smaller operations might lack the technical resources to manage multi-vendor integration effectively. For these cases, closed-stack solutions offer legitimate value. But for the majority of established mining operations with significant invested capital in mixed fleets, the integration complexity of open autonomy is a manageable challenge compared to the alternative of massive asset write-offs.
Open Autonomy Accelerates Innovation
The next breakthrough in autonomous mining might be five years away—or fifteen. The closed ecosystems may iterate faster within their own stack, they often limit the scope of innovation to what fits their proprietary roadmap. Open autonomy, on the other hand, fosters a broader innovation ecosystem where third-party developers, research institutions, and integrators can contribute breakthroughs that benefit the entire industry. Decoupling autonomy from equipment brands allows miners to adopt emerging technologies as they mature, without being limited by the timeline of a single vendor.
In the meantime, mines need to generate returns, control costs, and maintain competitiveness. The ability to preserve existing fleet investments while implementing autonomy provides immediate, quantifiable value that funds the adoption of future innovations.
Conclusion: Value in Hand
The debate over open versus closed autonomy often focuses on future possibilities, but for many mining operations, the most compelling argument lies in present realities. The ability to retain and autonomize mixed fleets doesn't just preserve capital—it maintains operational flexibility, leverages existing expertise, and provides a pragmatic path to automation that aligns with how mines actually operate. Autonomous mining is not a one-size-fits-all journey. For most operations, the path forward must be economically viable, operationally realistic, and strategically sound.
Mixed fleet retention powered by open autonomy delivers on all three.
It enables mines to:
- Protect existing fleet investments
- Maintain competitive sourcing
- Preserve operational expertise
- Achieve autonomy on their terms
Yes, integration is complex. But that complexity is solvable—with standards, partners, and proven technology. The alternative—discarding millions in productive assets—isn’t just inefficient. It’s avoidable.
Learn more about Wenco today
Interested in Wenco mining solutions? Reach out today to find answers to your questions, access more product information, or request a demo.