Mine contractors have to deal with challenges that owner-operated sites don’t.
The basic process for contractors working an open-pit site may be the same — dig, haul, and clean up — but the economics are very different.
Small contractors must be much more diligent than owner-operated sites.
All mining operations require care and attention. But, contractors lack the budgets, flexibility, and economies of scale that let large mining companies bounce back from a shift with reduced productivity. (They also often lack the most advanced systems that give these companies that advantage in the first place.)
Typically, contractors provide a fixed service for a fixed price. They remove overburden during mining pre-strip. They drill and blast a new bench before excavation. They manage production for a set period after site commissioning. They backfill mined-out areas during reclamation.
For these contractors, downtime and delays make an enormous difference to their bottom line. Every minute they sit idle eats into their profitability — with little chance to make up the difference.
Obviously, no operation likes to stall. But, large sites can absorb the impact better than contractors with constrained profits and limited equipment in reserve.
It’s why reliability is so important for contractors — not just for their equipment, but also for the systems they use to run them. They need their tools to work consistently — their business depends on it.
How system reliability differs from equipment reliability
Reliability for computer systems is similar to reliability for excavators and haul trucks. Durability of hardware, software quality, and access to technical support all contribute to the real metric: whether or not you can use your solution.
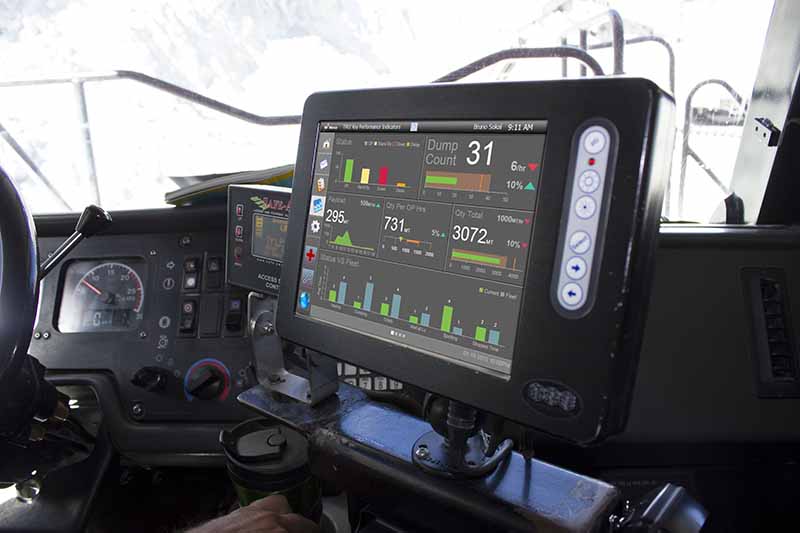
But, there are important differences to consider.
Heavy equipment is built to handle the rigors of the mining environment. Most computer systems are not. Therefore, ruggedized hardware is essential for technology in the mining industry — and not all ruggedization is created equal.
For starters, mining-ready hardware must be able to withstand a wide range of temperatures — −40°C to more than 60°C, at least. It must also be ready for temperature shock — the fluctuation from one temperature to another. Even if normal temperatures at your site hover around 25°C, you need to consider all the possibilities. You don’t want your entire operation to fail due to a cold snap or a heat wave.
Moisture and dust also need careful control through ruggedized seals, as either can lead to short circuits (and both are in ample supply on mine sites).
Mining-ready hardware also needs to compensate for vibration and shock. As trucks or dozers travel over rocky terrain and sustain impacts through regular use, their onboard hardware needs to keep recording and processing data.
But, any movement has the potential to cause your computers to malfunction. (If you’ve ever dropped your laptop, you know what can happen.) Ruggedized hardware for mining require exacting designs to protect your circuit boards, cables, and communication devices from hard, sudden bumps and regular, repetitive tremors.
Fortunately, industrial standards exist for all these parameters. The key for mines and mine contractors is to ensure their technologies meet them.
What about software quality?
Software quality makes an enormous difference to system reliability as well.
Everyone has tried an app that crashed constantly or used a clunky interface. With a smartphone game, it may not matter much. But, it’s a whole other issue if you’re using a bug-filled system to track your business’s operational data.
This is why quality management is such an important process for both vendors and their customers. Technologists like Wenco want to ensure their solutions work as intended, while mines and mine contractors need to trust their technologies receive appropriate scrutiny to minimize usability issues.
Mines — and especially mine contractors — would do well to source their technology from vendors who follow robust quality management protocols, such as those set out by ISO 9001:2015.
Technical support has a huge effect on system reliability
Of course, problems arise with even the best technology. It’s why any good solution comes paired with robust technical support. Without it, the reliability of your system is in jeopardy.
Two different elements go into technical support for mining systems:
- Access to expertise that can help restore functionality; and
- Access to replacement components as needed.
Both are important to ensure reliability.
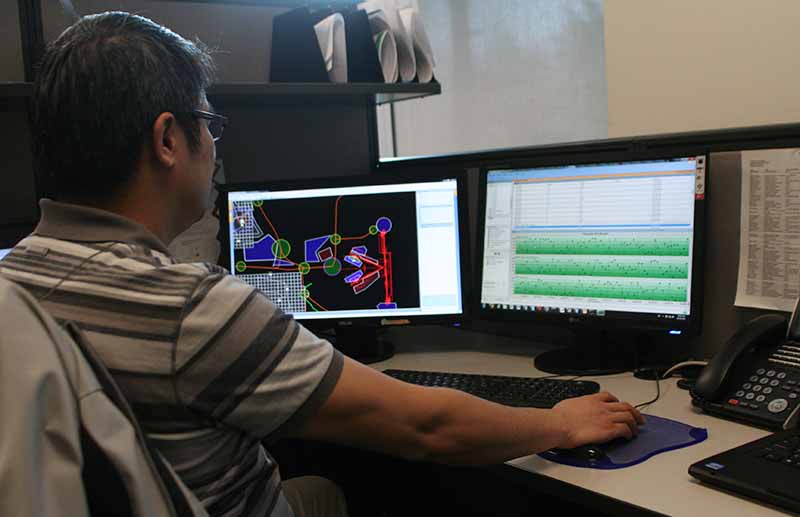
While the COVID-19 pandemic forced a lot of expert support from Wenco and other vendors to occur remotely, it simply hastened a trend already in progress. For years, Wenco customers have been asking for more flexible and physically distant support options. After all, mines are frequently located far away from major cities in countries with onerous visa regulations and transport infrastructure. In-person support could sometimes take days to arrive.
Now, remote support technologies have made it possible to deploy instant technical expertise anywhere with an internet connection — a major benefit to site personnel. They even enable a follow-the-sun approach, which delivers superior service to mines 24/7 — regardless of their location.
This change improves access to expertise, but what about access to spare parts? That’s where an open philosophy makes a real difference.
Commercial-off-the-shelf hardware can vastly raise overall system reliability. If a component fails, it’s much better for customers to have commodity parts available at warehouses nearby. Otherwise, they can get stuck needing a piece of proprietary hardware with a lead time of weeks or months. That goes double for contractors, who don’t typically have the luxury of warehouses with spare hardware in reserve.
The real KPI: Can you use your mining solution?
More and more mine contractors are finding value in digital technologies, especially as developments like cloud solutions and SaaS make them more accessible than ever before. It’s a welcome trend for the industry that more operations are able to increase their productivity and efficiency.
But even as these technologies see wider adoption, the considerations of adopting technology for contractors is still different from an owner-operated mine. Even while the goals are the same, contractors with thin margins need to consider priorities beyond cost and benefits claimed.
For many of them, reliability needs to remain top of mind.
Want to know more about Wenco’s solutions for mine contractors? Download The Wenco Guide to Machine Guidance for Mine Contractors.
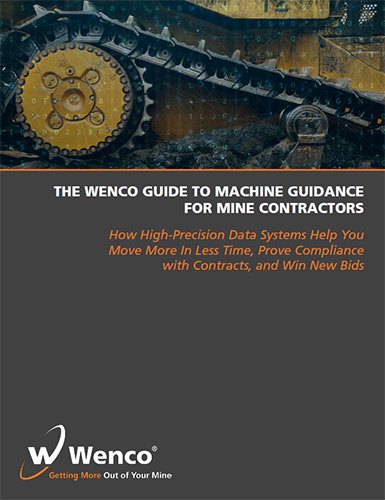
Inside, you'll learn about...
- How machine guidance works
- The top 3 ways contractors use machine guidance to raise their profitability
- The most common questions users have about machine guidance
- How this simple technology lowers wait times, automates data collection, and helps you land more contracts than ever before
Get The Wenco Guide to Machine Guidance for Mine Contractors now to learn how to improve your profitability today.