Modern mining is a complex process. Distinct departments, each with their own systems and procedures, need to work in concert to extract ore and convert it into a worthwhile commodity. The activities of block modeling, mine planning, drilling and blasting, loading and hauling, maintenance, crushing, beneficiation, and other areas can all affect the performance and productivity of one another.
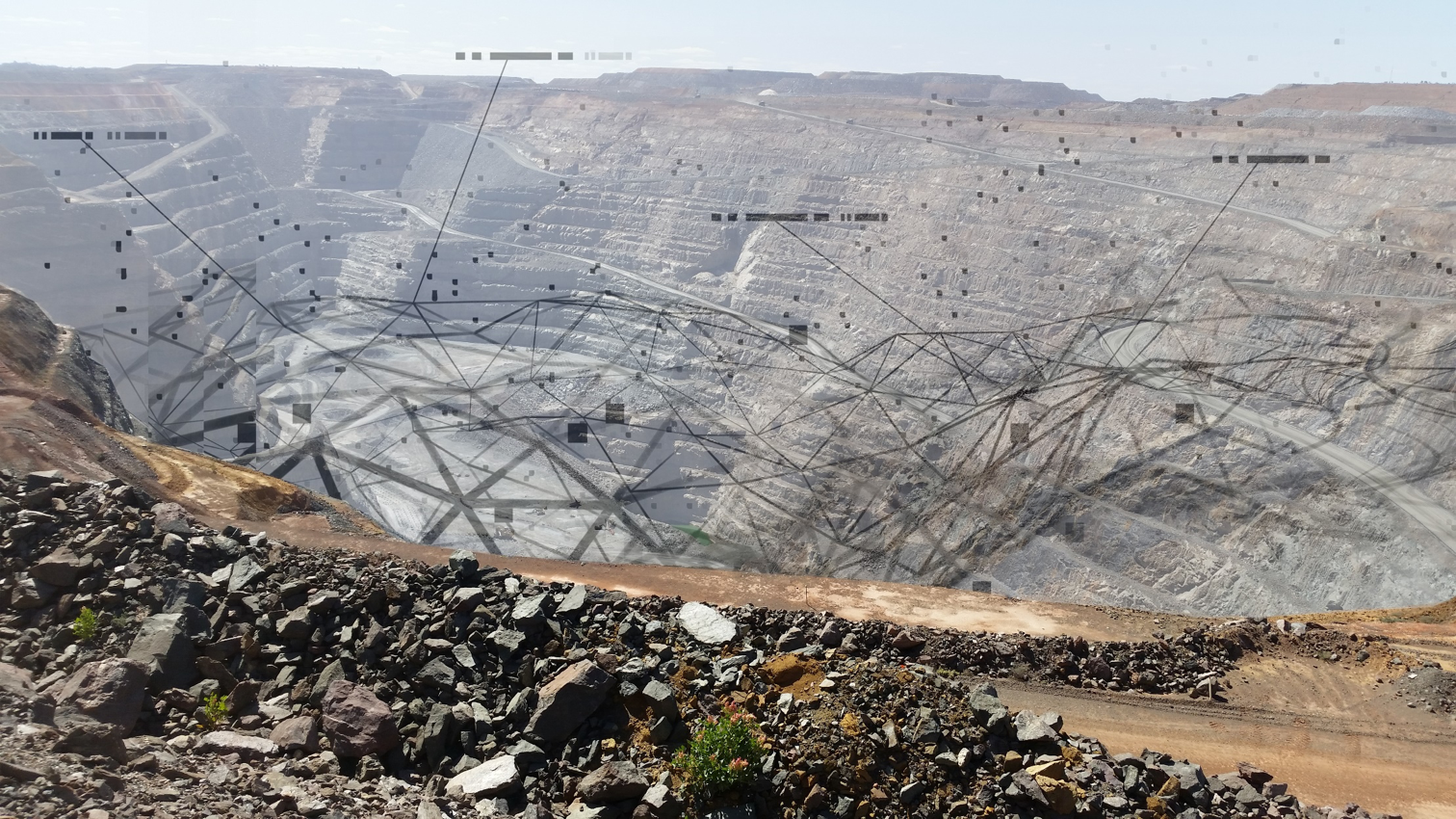
Thanks to the advent of Digital Mining, forward-thinking sites are now seeing the advantages of knocking down departmental silos and treating the entire mine as one cohesive unit. Lower operating costs. Improved health and safety. Continuous improvement across all business areas. But, many smaller-scale mining operations have yet to reap the benefits. Even though they understand the revolution possible through Digital Mining, the enterprise-level IIoT platforms involved in making it happen tend to extend beyond the scope of small mines, quarries, and contractor-run sites. Or, so they think. Mining technology has made significant jumps in recent years, offering Digital Mining solutions that can help any scale of operation — not just ones that can handle extensive infrastructure, overhead, and upkeep. Many small- to medium-size operations are finding significant ROI using data technologies that fit their unique business needs. Here are a few ways such mines are putting their data to work to extract unrealized value.
Correcting drill depths by detecting on-ground collar position
The drill-and-blast process can influence the efficiency of every aspect of mining down the line. Accurate drilling leads to effective blasting, which makes everything from road construction to excavation easier to handle. But, it all hinges on placing blast holes at the correct depths in the first place.
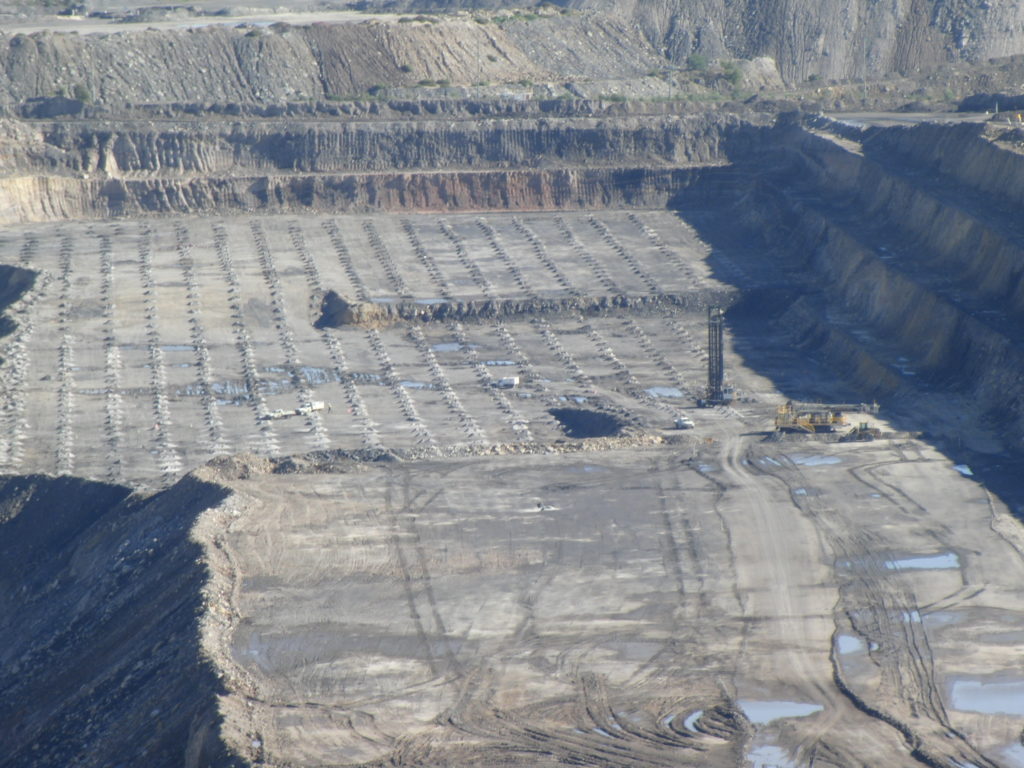
Manual methods can approximate drill pattern designs, but real-time data collection makes the process significantly faster and more precise. Advances in data technology allow a high-precision drill guidance system to place blast holes at exact GNSS coordinates without surveying or pattern marking. Onboard GNSS and tilt sensors direct drill operators as they tram to the location of the next hole in the pattern, then create a hole at the precise depth and angle. Solutions like the Wencolite drill system actually recalculate hole depths based on the on-ground collar position (which can stray significantly from original designs). In doing so, these drill systems improve the accuracy of as-drilled surfaces to maximize fragmentation and minimize throw. Typical blast holes using high-precision drills fall within ±5 cm of the intended design. Moreover, these systems record their as-drilled surface data for use in reporting, analysis, and further planning. Mines can compare planned-vs.-actual drill patterns in 3D, gaining insight into the challenges of the site's unique topography.Starting the mining process from an accurate position is an ideal low-cost entry point into Digital Mining for smaller operations. A quarry or contractor can acquire a single high-precision drill system and begin to see benefits immediately without any further investment.
Improving KPIs with automated data collection
Mine managers can set all the key performance indicators they want, but efforts are doomed to failure without reliable, accurate data. Recordkeeping that relies on Excel (or, worse, pen and paper) simply cannot gather data with the precision necessary to make trustworthy decisions that improve operational performance and sustain them for the long haul. Even the most diligent operator is prone to simple data entry errors that compound into big issues when repeated over the course of a year.
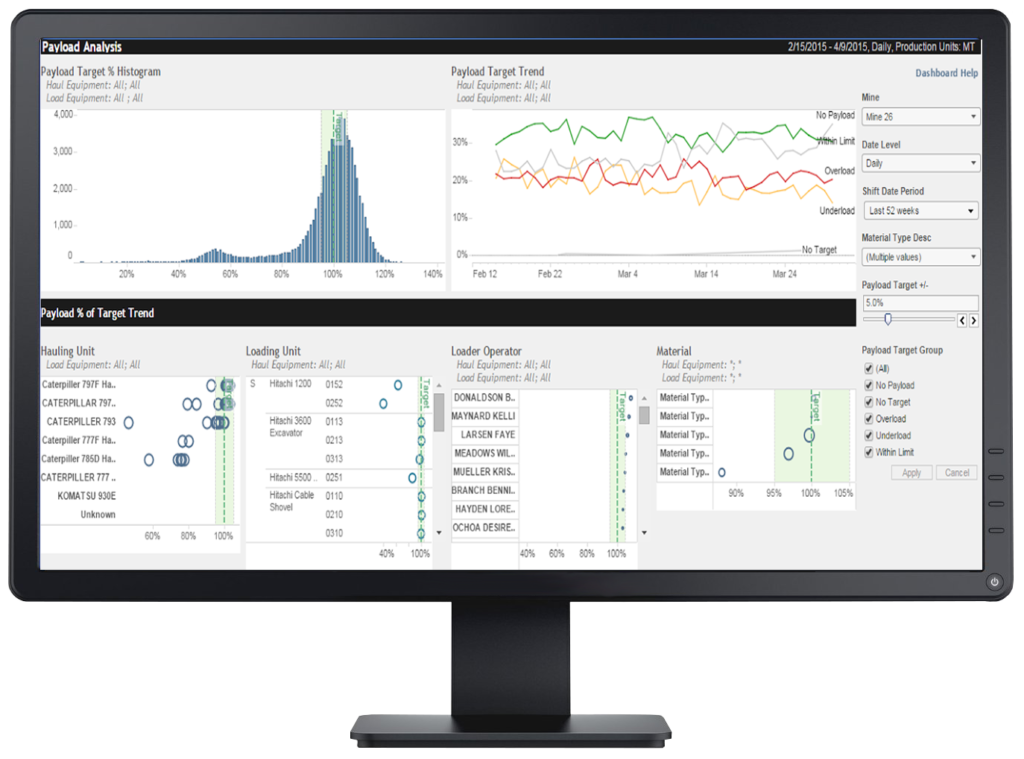
Unfortunately, many mines assume automated, accurate data collection requires an extensive network infrastructure and constant maintenance. But, thanks to steady improvements in technology, more and more operations have access to solutions that record and store thousands of data points each shift without such overhead.For example, the edge component of the Wencolite fleet management system sits on a mine's mobile fleet, collecting and communicating data across the operation in real time over a peer-to-peer-based wireless network. Essential KPIs such as drill rates, payload weights, and spotting times appear to operators immediately on the onboard display, storing onboard the device and loading at set intervals to the site's database. Through the system's integration with Wenco's Avoca Mining BI system, mines can then correlate this drilling, hauling, or cut/fill data with block models, mine plans, plant control data, and other data from third-party systems. Everything from shift reports to operator competency to long-range forecasting suddenly becomes much more accurate and effective. With Wencolite, these benefits come without all the additional infrastructure and specialized knowledge other solutions typically demand.
Safer and more efficient hauling through dozer cleanup
Once they have confidence in their data, mines gain access to a world of opportunities to improve operational performance. For example, they can rapidly determine sections of haul road in need of attention from dozers and bring them back into compliance with the urgency required.Any mine can configure the Wencolite eventing module to automatically trigger an alert when it detects certain equipment conditions, such as a sudden braking event. In the case of sudden braking, the system's edge component detects the swift drop in speed and records it to inform the site manager or superintendent.
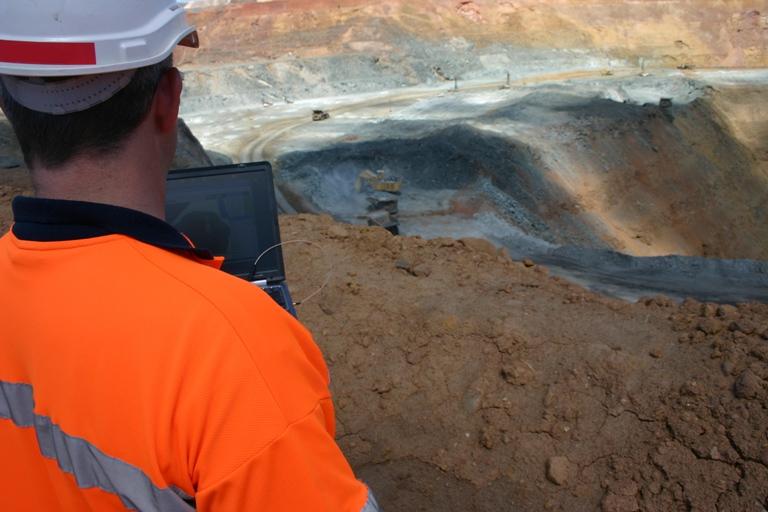
Because superintendents trust this alert is valid, they can then travel to that stretch of haul road in a survey vehicle to investigate the root cause of this issue. Typically, the cause of a sudden braking event is obvious — perhaps the road is washed out from heavy rains or rocks from a loaded haul truck have fallen to block the path. In these cases, superintendents can easily dispatch a data-powered high-precision dozer to bring the road back into specifications in a few passes.Still, sometimes the cause of a sudden braking event is more subtle — perhaps steep grading provokes operators into braking suddenly, but only when road visibility is compromised. Such a situation can prove difficult to diagnose, but a high-precision survey vehicle can quickly determine whether or not a road design complies with specifications. In this way, the mine is able to use its data intelligence capabilities to identify and resolve a major safety and productivity hazard much more rapidly and efficiently than manual surveying and earthmoving. These high-precision survey vehicle and dozer solutions communicate peer-to-peer, enabling the quick and easy setup ideal for small-scale operations.
A world of opportunities for small mines, quarries, and contractors
These options stand out among all the ways small- to medium-size mines, quarries, and contractors can make progress with Digital Mining. But, opportunities continue at every point in the mining value chain. From initial core sample assays to final shipment, all mines can take advantage of increased data collection, aggregation, and intelligence to streamline processes and smooth inefficiencies. Regardless of the scale of operation, solutions exist that can demonstrate ROI now and establish good data handling for further advancements in data interoperability and automation.
Want to learn more about Digital Mining for small- to medium-size mines, quarries, and contractors? Please contact us at info@wencomine.com or 604-270-8277.